“11800TEU集裝箱船出塢完整性達到97.8%、下水完整性均達到99%,40萬噸超大型礦砂船(VLOC)首制船出塢完整性達到97.76%,在建船舶分段無余量制造率達90%以上,部分分段建造預舾裝完整率接近100%……”這一組在船舶建造過程中經(jīng)過多年磨合、自我加壓才逐步達到的數(shù)據(jù),折射出江蘇揚子江船業(yè)集團公司全體員工在造船實戰(zhàn)過程中探索、積累的一套精益生產(chǎn)“真經(jīng)”,凝結(jié)了縮短船塢周期、提高下水完整性、提升分段無余量搭載、提升精度控制水平等方面的亮點。
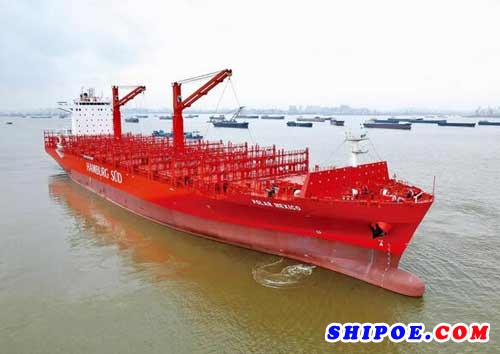
近年來,揚子江船業(yè)以建立現(xiàn)代造船模式為主線,從深化生產(chǎn)設(shè)計入手,積極推行精益造船和綠色造船,并建立中間產(chǎn)品完整性和期量標準,進一步提升造船總裝化程度和造船管理效率,使企業(yè)各項造船管理指標走在全國同行業(yè)前列。特別是在深化精益管理過程中,揚子江船業(yè)多措并舉提高下水完整性的做法頗具特色。
優(yōu)化設(shè)計
提高下水完整性
下水完整性的提高是縮短船舶建造周期、提升生產(chǎn)管理水平的具體體現(xiàn)。在揚子江船業(yè),技術(shù)部門通過優(yōu)化生產(chǎn)設(shè)計標準,提高生產(chǎn)設(shè)計圖紙準確率,完善各專業(yè)材料報購機制、及時處理現(xiàn)場問題等手段,為生產(chǎn)部門按計劃均衡組織生產(chǎn)創(chuàng)造條件。
“優(yōu)化工藝設(shè)計,在設(shè)計階段充分考慮工序前移,盡量做到能在平面安裝的部件不到立面去裝,能在分段安裝的部件不到合攏階段去裝,能在水上安裝的部件不到水下去裝,力求達到水上安裝、水下調(diào)試的目的。”揚子江船業(yè)所屬江蘇新?lián)P子造船有限公司一位資深管理干部告訴記者,圍繞縮短周期,揚子江船業(yè)每年都針對當年的船型,確定每個船型從開工、入塢、下水,直至交船的周期指標。比如,在1668TEU集裝箱建造過程中,該公司面臨諸多困難。最終,經(jīng)過項目組全體人員通力合作,使該船實際船臺周期達57天,比計劃提前3天;實際碼頭周期達88天,比計劃提前2天。因為該船的水上周期、水下周期以及碼頭周期均達到各項苛刻的指標要求,企業(yè)給該船項目組獎勵5萬元。
揚子江船業(yè)為新加坡太平船務有限公司建造的第九、第十艘11800TEU集裝箱船在其子公司揚子鑫福造船有限公司建造,這2艘船出塢完整性達到97.47%,創(chuàng)造了同型系列船出塢完整性最高紀錄。該管理干部表示,出塢完整性的進一步突破得益于生產(chǎn)設(shè)計的不斷深化,得益于企業(yè)各部門間的協(xié)同作戰(zhàn),得益于生產(chǎn)組織管理部門的執(zhí)行力。以11800TEU集裝箱船上建無余量搭載為例,這2艘船上建由于總組場地限制需要進行疊加總組,吊裝前需吊離942G分段后再進行901G分段吊裝,兩船上建共4吊,從開始吊裝至定位結(jié)束僅用11小時,且定位后即刻進入焊前交驗,比傳統(tǒng)吊裝模式至少節(jié)省60小時,為釋放龍門吊壓力及提升塢內(nèi)完整性提供了有力保障。此外,這2艘船無余量搭載率在前幾個批次經(jīng)驗積累的基礎(chǔ)上又得到了提升,總組階段無余量堪劃修割準確率從上一艘船的85%提高到96.4%,為兩船上建吊裝后快速進行結(jié)構(gòu)消化贏得了時間——兩船上建從吊裝到結(jié)構(gòu)、火工、窗戶沖水一次性完工交驗僅僅用了10天。同時,該批次上建吊裝前的完整性也創(chuàng)歷史新高。
“圍繞開工、上船臺、下水、交船四大節(jié)點,企業(yè)制定了嚴格的大計劃紅線,每一位管理干部和一線員工圍繞大節(jié)點計劃千方百計保節(jié)點、抓精度、提質(zhì)量,以強大的執(zhí)行力不斷提高中間產(chǎn)品完整性和造船精度管理水平。”該管理干部表示,揚子江船業(yè)向精益管理要效率,不斷縮短船塢周期、碼頭周期,并通過轉(zhuǎn)變經(jīng)營生產(chǎn)理念,深化改革,逐步形成特色鮮明、競爭力強的管理體系和生產(chǎn)模式。
引進軟件
推動管理走向數(shù)字化
引進生產(chǎn)管理系統(tǒng)軟件(YSS)作為生產(chǎn)管理的輔助手段,推動生產(chǎn)管理由粗放的經(jīng)驗管理模式向精細的數(shù)字化管理模式轉(zhuǎn)換,是揚子江船業(yè)近幾年增強企業(yè)軟實力、向管理要效益的管理升級之舉。
2014年,揚子江船業(yè)引進韓國YSS軟件系統(tǒng),并成功在企業(yè)應用,促進企業(yè)在生產(chǎn)管理過程中實現(xiàn)質(zhì)的飛躍。該管理干部表示,YSS系統(tǒng)使生產(chǎn)過程可視化,一改過去派工單、紙質(zhì)化的粗放式生產(chǎn)模式,通過該系統(tǒng)可以“一鍵”了解生產(chǎn)現(xiàn)場全貌,大到看板系統(tǒng)中的大日程、中日程、小日程,小到一線作業(yè)日報、派工單,均在系統(tǒng)內(nèi)生成,這對“大兵團”作戰(zhàn)的企業(yè)提升生產(chǎn)管理效率意義重大,對計劃控制、員工組織、工時管理、成本控制等也起到重要作用。他強調(diào),該系統(tǒng)能夠在揚子江船業(yè)成功應用,得益于企業(yè)強大的執(zhí)行力,依靠每一位管理人員、一線施工人員、外協(xié)班組的通力配合,也是全體人員保節(jié)點、抓精度、提質(zhì)量的集中體現(xiàn)。目前,該系統(tǒng)在新?lián)P子造船、揚子鑫福造船等實體子公司運行,通過3年多的推進已初步形成管理格局。
此外,為了進一步提高船舶下水完整性,揚子江船業(yè)各部門通力合作,重點在加強生產(chǎn)準備、強化過程管理等方面開展工作。特別是在40萬噸VLOC、10000TEU集裝箱船等系列船的建造過程中,各項目組制定了相應的下水完整性標準,并根據(jù)區(qū)域量化指標,促進工序前移。同時,為了提高下水完整性,該公司圍繞主機、管電舾配套等難點問題組織專題研究。
揚子江船業(yè)建造交付的10000TEU集裝箱船已經(jīng)成為該公司的品牌船型。在該型船的建造過程中,該公司嚴格遵循建造要求,組織生產(chǎn)管理部、質(zhì)量管理部、設(shè)計工藝研究所和相應的車間落實每一道工序的準備工作,并實時檢查,為建造工作的順利開展鋪平道路。為了提高10000TEU集裝箱船的中組完整性,尤其是機艙、艉部總段完整性,揚子江船業(yè)要求在中組階段完成管電舾預裝、設(shè)備安裝、涂裝施工等;在合攏階段控制總段狀態(tài)和生產(chǎn)節(jié)奏,按區(qū)域分階段設(shè)定完整性施工的目標,不斷細化總段、區(qū)域完整性施工日程計劃。同時,還積極推廣應用主機提前吊裝工藝、優(yōu)化舵軸系安裝工藝等,不斷摸索10000TEU集裝箱船在合攏階段的生產(chǎn)規(guī)律,以控制船塢周期,提高下水完整性。
未來,揚子江船業(yè)還將不斷提高建造質(zhì)量和管理水平,確保安全、確保品質(zhì)、確保交期,并根據(jù)市場和客戶需求,進一步加快科技創(chuàng)新,持續(xù)深化精益生產(chǎn),不斷提高船舶建造質(zhì)量和建造效率,用品質(zhì)塑品牌,用效率保效益,朝著“世界最優(yōu)秀船廠”的目標砥礪前行。
案例一
11800TEU集裝箱船出塢完整性高達97.8%
廠編N1212號11800TEU集裝箱船是揚子江船業(yè)所屬新?lián)P子造船為新加坡PIL公司建造的系列船中的一艘,該船塢內(nèi)周期126天,且出塢完整性達到所有同型船中最好的狀態(tài),船塢車間完工量100%、甲裝車間100%、涂裝車間100%、機電車間95.26%,綜合完整性達97.8%。
11800TEU集裝箱船多項指標突破該型船歷史紀錄,得益于揚子江船業(yè)在該船涂裝、機電等方面全力以赴搶工期、提精度。在涂裝方面,該公司打破以往的施工習慣和思路,首次完成對煙囪內(nèi)外油漆施工結(jié)束后吊裝。該船在塢內(nèi)固化了上建外表油漆完工拆架,所有的內(nèi)部區(qū)域打磨油漆施工結(jié)束轉(zhuǎn)內(nèi)裝插板;綁扎橋、箱柱的面漆施工結(jié)束并拆架;錨鏈艙完工封艙,錨鏈入艙;貨艙壁、橫艙壁、橫艙壁上空艙的完整性施工結(jié)束;淡水艙、蒸餾水艙、飲用水艙的拆架、完工等也取得突破。
在機電方面,該船機艙26個艙、7個柜子封閉報檢結(jié)束,管裝系統(tǒng)安裝密性全部報檢結(jié)束,除主機滑油(投水結(jié)束)外其余投油全部報檢結(jié)束。主配電板、應急配電板和集控臺相關(guān)設(shè)備安裝結(jié)束,通電結(jié)束,機艙監(jiān)測系統(tǒng)具備開通條件,機艙集控室和上建7層電纜完工報檢,內(nèi)裝封板,照明亮化等。
N1212號11800TEU集裝箱船在建造過程中,經(jīng)歷高溫及連續(xù)陰雨天氣,但在該公司各車間、部門的自我加壓、通力配合下,塢內(nèi)完成程度超過了預期目標,不僅提高了出塢完整性,創(chuàng)造了11800TEU集裝箱船系列船完整性歷史最高紀錄,而且對縮短水下調(diào)試周期起到了積極的推進作用。
案例二
舾裝墊板分段預裝 精度控制顯成效
在船舶建造過程中,分段舾裝墊板因安裝數(shù)量多、規(guī)格多、結(jié)構(gòu)小,且受分段建造狀態(tài)限制,普遍在分段脫胎后進行安裝,對精度尺寸控制要求較高,以前舾裝墊板錯裝、漏裝情況較普遍,造成合攏階段大量返工修正和油漆破壞。
為提高舾裝墊板安裝精度,揚子江船業(yè)分段車間將舾裝墊板納入車間質(zhì)量重點控制項目并組織落實相應管理措施。一方面,統(tǒng)一舾裝墊板劃線基準,劃線時參照分段基準線減少累計誤差;另一方面,將舾裝墊板劃線安裝列入精度單列報檢項目,實施嚴格的項目報檢制度。此外,結(jié)合現(xiàn)場施工情況,不定期組織現(xiàn)場施工人員進行定位安裝培訓。通過專項重點項目管理推進,分段舾裝墊板安裝精度顯著提高,其中,40萬噸VLOC首制船及在建船的舾裝墊板精度實現(xiàn)零失誤,取得了較好的控制效果。